AI in Manufacturing: Enhancing Production Efficiency
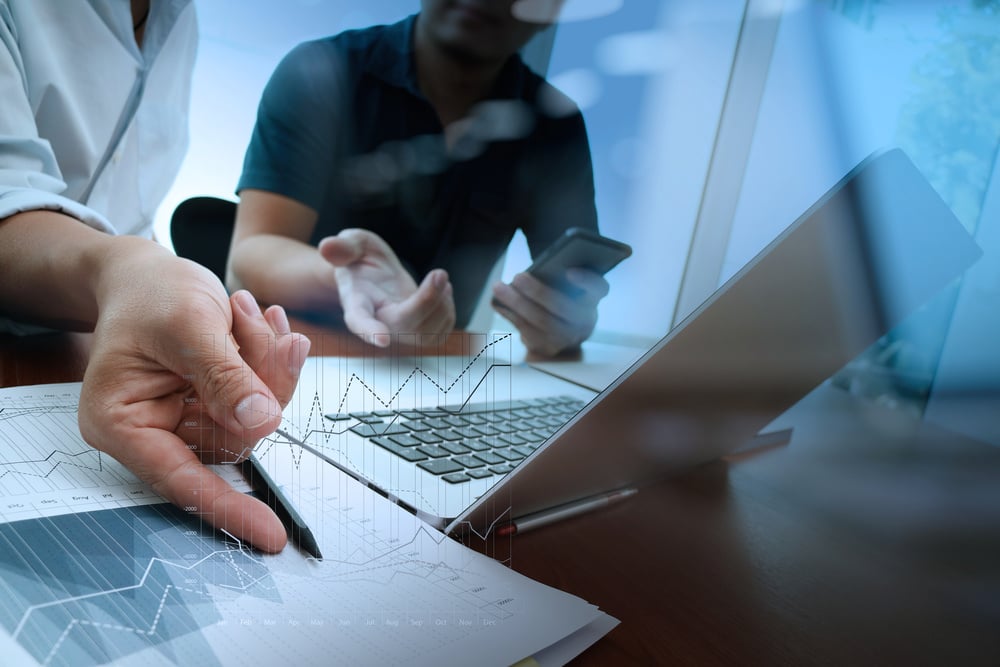
Smart robots work with people on factory floors. They do tasks that are hard or dangerous for humans. AI also helps design new products and manage supply chains. It uses data to make smart choices about what to make and when. AI contributes significantly to supply chain resilience by improving responsiveness and agility, helping companies manage demand fluctuations and optimize inventory.
Companies that use AI in manufacturing are seeing good results. They can make custom products faster and cheaper. AI capability enhances various manufacturing processes, including workforce planning, predictive maintenance, and production scheduling. AI helps them use less energy and materials too. This is good for the environment and saves money.
Key Takeaways
-
AI enhances manufacturing speed, quality, and efficiency
-
Smart robots and humans work together in modern factories
-
AI solutions help companies save money and reduce waste
Basics of AI in Manufacturing
AI is transforming manufacturing by automating processes and improving efficiency. It uses data and algorithms to make production smarter and more responsive.
Definition of AI
AI in manufacturing refers to computer systems that can perform tasks that usually need human intelligence. These systems can learn from data, spot patterns, and make choices with little human input.
AI includes machine learning, which allows computers to improve their performance over time. It also covers robotics, computer vision, and natural language processing. AI-driven predictive maintenance is a transformative technology for manufacturers, allowing them to predict equipment failures, reduce downtime, and improve operational efficiency.
In factories, AI can control machines, check product quality, and plan production schedules. It makes decisions based on real-time data from sensors and other sources. AI algorithms optimize operations through performance monitoring, real-time data analysis, and predictive maintenance by identifying patterns and trends.
Role of AI in Modern Manufacturing
AI plays a key role in making factories smarter and more productive. It helps companies make better products faster and with less waste.
Some key AI applications in manufacturing include:
-
Predictive maintenance: AI predicts when machines will need repairs, reducing downtime. Digital twins play a crucial role in simulating and optimizing the performance of physical assets through real-time data from sensors.
-
Quality control: AI-powered cameras spot defects humans might miss.
-
Supply chain optimization: AI forecasts demand and manages inventory more accurately.
-
Robot control: AI makes robots more flexible and able to work safely alongside humans.
AI also helps with product design and testing. It can suggest improvements and simulate how new products will perform. Generative design software, powered by AI, accelerates design iterations by aligning with specific business objectives, leading to innovative product designs that meet market demands.
By using AI, manufacturers can respond faster to changes in demand or supply. This makes them more competitive in today’s fast-paced market.
The Manufacturing Value Chain and AI
AI is transforming every stage of manufacturing. On the shop floor, AI enhances operational efficiency by monitoring machinery, optimizing layouts, and ensuring safety. It helps companies make smarter decisions, boost efficiency, and improve quality across their operations.
The transformative impact of artificial intelligence on manufacturing processes is evident in predictive maintenance, supply chain optimization, and quality control. AI technologies drive advancements and help achieve sustainability goals within manufacturing processes.
Supply Chain Optimization
AI tools analyze data from suppliers, inventory, and customer demand. This helps companies predict needs and avoid shortages. Machine learning spots patterns humans might miss. It can suggest when to order materials and how much. Additionally, manufacturing solutions that utilize AI enhance supply chain management by improving efficiency, accuracy, and cost-effectiveness.
AI also improves logistics. It finds the best shipping routes and predicts delivery times. This cuts costs and gets products to customers faster. However, implementing AI in supply chain optimization comes with challenges, such as the need for a clear strategy and addressing integration issues to ensure successful adoption.
Smart algorithms help manage warehouse operations too. They decide where to store items and how to pick them efficiently. Some warehouses use AI-powered robots to move products around.
Production and Operations
On the factory floor, AI makes manufacturing smarter and more flexible. Computer vision systems inspect products for defects. They work faster and more accurately than human eyes.
AI also helps with predictive maintenance. It analyzes data from sensors on machines. This spots problems before they cause breakdowns. It saves time and money on repairs. Additionally, AI analyzes market trends to optimize production schedules, ensuring efficient resource allocation and timely responses to demand changes.
Collaborative robots work alongside humans. They handle repetitive or dangerous tasks. This improves safety and frees up workers for more skilled jobs. AI enhances human capabilities in manufacturing by identifying defects beyond human capabilities and augmenting workers' efficiency and safety.
AI optimizes production schedules too. It balances workloads and adjusts for unexpected events. This keeps production lines running smoothly.
After-Sales and Services
AI enhances customer support after products are sold. Chatbots answer common questions quickly. They can handle basic troubleshooting too. Integrating AI in after-sales services can further personalize customer interactions and streamline issue resolution.
For more complex issues, AI helps human agents. It suggests solutions based on past cases. This speeds up problem-solving.
Predictive analytics spot potential product issues early. Companies can fix problems before customers notice. This builds trust and loyalty. Additionally, digital twin technology plays a crucial role in enhancing product quality and customer satisfaction by simulating real-world conditions and enabling proactive decision-making.
AI also helps companies design better products. It analyzes data from returned items and customer feedback. This shows what features work well and what needs improvement.
AI-Driven Quality Assurance and Control
AI is transforming quality assurance and control in manufacturing. For instance, a real-world example is Foxconn, which uses AI to enhance quality assurance by identifying defects in real-time during the production process. It helps catch defects early and keeps machines running smoothly. This leads to better products and less downtime.
Additionally, AI enables data-driven decisions in quality control by analyzing historical data and market trends to predict potential issues and optimize processes.
Predictive Maintenance
AI systems can predict when machines will need repairs. They look at data from sensors and past breakdowns. This helps factories fix issues before they cause problems. Additionally, AI provides data-driven insights for predictive maintenance, allowing for more accurate and timely interventions.
Machine learning models analyze vibrations, temperatures, and other signals. They spot patterns that humans might miss. When something looks off, the AI alerts technicians. AI can also predict demand for maintenance resources, ensuring that necessary parts and personnel are available when needed.
This approach cuts surprise breakdowns. It also saves money on unnecessary maintenance. Factories can plan repairs during slow times. This keeps production going and improves quality.
Defect Detection Systems
AI-powered cameras and sensors find product flaws quickly. They check items on assembly lines faster than human eyes. This catches more defects before products leave the factory. AI algorithms play a crucial role in defect detection by analyzing real-time data and identifying patterns that indicate potential issues.
These systems use computer vision and deep learning. They’re trained on thousands of images of good and bad products. The AI can spot tiny issues a person might not see. AI agents assist in identifying and managing defects by utilizing advanced technologies to optimize the inspection process and minimize human intervention.
As products move down the line, the AI checks each one. It flags items with problems for further inspection. This helps ensure only high-quality goods reach customers.
AI defect detection works 24/7 without getting tired. It can handle high-speed production lines. This leads to more consistent quality control.
Technological Innovations in AI Manufacturing
AI is transforming manufacturing through smart factories, advanced 3D printing, and intelligent robots. By analyzing real-time sensor data, businesses can identify equipment issues before they escalate into failures, thereby enhancing operational efficiency and reducing downtime. These technologies are making production more efficient, flexible, and precise.
AI technologies, such as automation and data analysis, are also enhancing efficiency by streamlining operations, improving process accuracy, and reducing costs. This leads to more adaptable and responsive manufacturing systems.
Smart Factories
Smart factories use AI to connect machines, systems, and processes. Sensors gather data from equipment in real-time. AI analyzes this data to optimize production, contributing to cost efficiency by reducing operational costs and streamlining processes.
Predictive maintenance prevents breakdowns before they happen. AI spots patterns that signal future problems. This keeps production running smoothly and helps optimize efficiency within factory operations.
AI also adjusts factory operations automatically. It can change production speeds or switch product types quickly. This helps factories respond fast to demand changes.
Quality control improves with AI-powered visual inspection systems. These catch defects human eyes might miss. The result is higher quality products with less waste.
Additive Manufacturing and AI
AI is making 3D printing smarter and more capable. It helps design parts that are lighter yet stronger. AI can suggest design improvements humans might not think of. Digital twin technology plays a crucial role in additive manufacturing by creating virtual replicas of the printing process, enabling simulation and analysis for performance optimization.
Printers guided by AI create complex shapes impossible with traditional methods. They can print parts with internal structures that save material and weight. Generative design software enhances 3D printing processes by allowing for the rapid exploration of multiple design iterations based on specified objectives, leading to optimized and innovative product designs.
AI monitors the printing process in real-time. It adjusts settings to ensure perfect results. This reduces errors and improves part quality.
Smart software plans the most efficient way to print multiple parts. It arranges them to use materials wisely and print faster.
Robotics and Automation
AI-powered robots are becoming more flexible and easier to use. They can now handle delicate tasks and work safely alongside humans. An AI system plays a crucial role in optimizing robotic operations by enabling precise control and adaptability.
Collaborative robots, or cobots, learn new jobs quickly. AI helps them adapt to changes without reprogramming. This makes automation practical for smaller companies. Additionally, AI helps optimize manufacturing processes through automation, making factory operations more efficient and responsive to demand.
Computer vision lets robots “see” their surroundings. They can pick parts from bins, avoiding collisions. Some robots can even identify and sort different objects.
AI helps robots understand human speech and gestures. This makes it easier for workers to give instructions or work together with robots on complex tasks.
Data-Driven Decision Making
AI helps factory managers make smarter choices using real-time data and predictive analytics. By collaborating with human workers, AI can enhance decision-making processes, combining human intuition with machine precision. This leads to better planning, faster problem-solving, and more efficient operations.
Analyzing data is crucial for making informed decisions. AI leverages historical sales data and market trends to optimize stock levels, forecast future needs, and respond effectively to market fluctuations, thereby minimizing costs and increasing efficiency.
Big Data Analytics
AI systems crunch huge amounts of data from sensors, machines, and other sources. They spot patterns humans might miss. This helps managers see the big picture and make informed decisions. Additionally, AI automates routine tasks in data analysis, allowing analysts to focus on more complex insights.
AI tools can predict equipment failures before they happen. This lets factories schedule maintenance at the best times. It cuts downtime and saves money. Moreover, AI plays a crucial role in managing raw materials in manufacturing, streamlining the journey from raw materials to finished products.
These systems also help optimize production schedules. They look at factors like orders, inventory, and staffing. Then they suggest the most efficient ways to run the factory.
Real-Time Monitoring
AI watches factory operations as they happen. It alerts managers to issues right away. This quick feedback lets them fix problems fast. Additionally, AI helps identify patterns in real-time data, improving operational efficiency and decision-making.
Smart cameras and sensors keep an eye on production lines. They can spot defects or slowdowns instantly. Managers can then take action to keep things running smoothly. AI also optimizes energy consumption in manufacturing by analyzing usage patterns and recommending adjustments, contributing to cost reduction and sustainability.
AI also tracks worker safety in real-time. It can warn about dangerous situations or remind staff to use safety gear. This helps prevent accidents and keeps everyone safer.
AI in Manufacturing Operations and Efficiency
AI boosts factory productivity and cuts costs. Manufacturing engineers play a crucial role in utilizing AI technology to enhance production processes by making design assumptions about equipment operation and using sensor data to capture actual usage for better operational efficiency. It helps make operations run smoother and use less energy.
Manufacturing AI significantly impacts operational efficiency by enabling predictive maintenance and quality control, helping manufacturers modernize processes and stay competitive in a rapidly evolving market.
Operational Efficiency
AI systems watch production lines closely. They spot problems early and fix them fast. This keeps machines running longer without breaks. In the manufacturing sector, AI significantly enhances efficiency, quality control, and decision-making processes.
Smart robots work alongside people. They do repetitive tasks quickly and safely. This frees up workers for more skilled jobs. Manufacturing companies are increasingly adopting AI to enhance efficiency, reduce costs, and streamline processes.
AI also plans production schedules. It looks at orders, supplies, and worker availability. Then it makes the best plan to meet deadlines.
Quality control gets better with AI vision systems. They check products faster and more accurately than human eyes. This means fewer defects slip through.
Energy and Cost Savings
AI helps factories use less power. Smart systems adjust lighting and heating based on activity. They turn things off when not needed.
AI also enhances demand forecasting for better inventory management. By analyzing historical data, AI predicts demand fluctuations, optimizes inventory, and improves overall operational efficiency.
Predictive maintenance saves money. AI checks machine health and predicts breakdowns. Repairs happen before costly failures occur.
Energy-hungry processes get optimized. AI fine-tunes settings to use the least power possible. This cuts electricity bills.
AI optimizes production processes to reduce costs. By utilizing advanced technologies such as machine learning and IoT systems, AI improves workflows, reduces downtime, and adapts to changing demands.
Supply chain management improves with AI. It finds the best suppliers and delivery routes. This reduces waste and lowers costs.
Challenges and Considerations For AI Integration
AI adoption in manufacturing brings major benefits but also important hurdles. Companies must carefully plan for technical, safety, and ethical issues as they integrate AI systems. One of the key benefits of AI integration is its ability to analyze large data sets, aiding manufacturers in making informed decisions that align with market demands and streamline the design process.
AI agents play a crucial role in overcoming integration challenges by utilizing advanced technologies like AI and machine learning to optimize manufacturing processes. These agents enable companies to enhance throughput and minimize operational costs with minimal human intervention.
Complexity of Implementation
AI implementation in factories can be tricky. Many manufacturers struggle with data quality problems. AI models need lots of clean, labeled data to work well. Old equipment may not collect the right information. Connecting different systems and machines is hard too. The importance of sensor data for AI implementation cannot be overstated, as it helps in optimizing assembly lines and conducting predictive maintenance.
Staff training is another big task. Workers need new skills to use AI tools. This takes time and money. Some employees might worry AI will replace their jobs. Embedding AI in manufacturing workflows also presents challenges, such as data quality issues and the need for customization, which can discourage manufacturers despite recognizing its potential.
AI models can also be hard to understand. Their decision-making isn’t always clear. This “black box” problem makes it tough to spot and fix errors.
Safety and Ethics
AI in manufacturing raises safety concerns. Robots and machines guided by AI could hurt workers if something goes wrong. Manufacturers must put in place strong safeguards. Additionally, the integration of AI in the assembly process brings up safety concerns, as cobots and other technologies must be carefully managed to prevent accidents and ensure worker safety.
There are also worries about privacy. AI systems collect lots of data. Companies need to protect worker and customer information. They should be clear about what data they gather and how they use it.
Bias in AI is another issue. If training data isn’t diverse, AI might make unfair choices. This could lead to discrimination in hiring or other areas. Manufacturers should check their AI for bias regularly. Furthermore, ethical considerations in the manufacturing process involving AI must be addressed to ensure that automation and data usage do not compromise ethical standards.
The Future of AI in Manufacturing
AI is set to reshape manufacturing in the coming years. AI innovation will enhance collaboration between humans and robots, making tasks safer and more efficient through smarter technology. New capabilities and trends point to a more automated and efficient industry. Smart manufacturing, integrating AI technologies, will enable real-time data analytics, predictive maintenance, and automation, transforming traditional processes into intelligent, adaptive systems that maximize productivity and minimize waste.
Trends and Predictions
AI adoption in manufacturing is accelerating rapidly. Many companies are moving beyond research to put AI into production. By 2028, experts predict the AI manufacturing market will grow to over $20 billion. The impact of AI on the manufacturing industry is profound, enhancing productivity and efficiency through applications like predictive maintenance and supply chain optimization.
More factories will use AI for quality control, predictive maintenance, and supply chain optimization. Digital twins will become common, allowing companies to test changes virtually before implementing them. AI also plays a crucial role in demand forecasting, analyzing historical data to predict demand fluctuations, optimize inventory, and improve overall operational efficiency.
Robotic production lines directed by AI will increase. This may lead to faster, more precise manufacturing processes. However, humans will still play key roles in overseeing and working alongside AI systems.
Evolving AI Capabilities
AI in manufacturing is becoming more advanced. Future AI may be able to design products, manage entire production cycles, and make complex decisions. Additionally, advancements in AI are optimizing production processes, enhancing efficiency, accuracy, and flexibility in various manufacturing contexts.
Machine learning will improve, letting AI systems learn from data and experiences. This could lead to smarter robots and more flexible production lines. The key benefits of evolving AI capabilities include the ability to analyze large data sets, aiding manufacturers in making informed decisions that align with market demands and streamline the design process.
Natural language processing may allow workers to give voice commands to machines. Computer vision advances could enhance quality inspections and safety monitoring.
As AI capabilities grow, manufacturers will need new strategies to integrate these technologies. Training workers to use AI tools will be crucial for successful adoption.
Case Studies: AI Success Stories in Manufacturing
AI is transforming manufacturing with real-world results. Two leading companies, GE and Siemens, showcase how AI boosts efficiency and quality. AI agents play a crucial role in these success stories by utilizing advanced technologies to optimize manufacturing processes, enhancing throughput, and minimizing operational costs with minimal human intervention.
In various case studies, the importance of sensor data is highlighted. By analyzing real-time sensor data, businesses can identify equipment issues before they escalate into failures, thereby enhancing operational efficiency and reducing downtime.
General Electric (GE)
GE uses AI to optimize its jet engine production. The company’s “Brilliant Factory“ concept combines sensors, data, and analytics to improve operations. Manufacturing AI has significantly enhanced GE's operational efficiency and product customization, making it a transformative force in their manufacturing processes.
AI-powered systems monitor equipment in real-time. This helps predict maintenance needs before breakdowns occur. As a result, GE has cut downtime by up to 20% in some plants. Additionally, GE uses AI for analyzing data to optimize production, leveraging historical data and market trends to make informed decisions.
The company also uses AI for quality control. Computer vision systems inspect parts faster and more accurately than humans. This has reduced defects by up to 25% in certain production lines.
GE’s AI initiatives have led to significant cost savings. The company reports over $1 billion in productivity gains since implementing these technologies.
Siemens
Siemens applies AI across its manufacturing processes. The company’s “Digital Enterprise” platform integrates AI into design, production, and maintenance. AI significantly impacts the manufacturing sector by enhancing efficiency, quality control, and decision-making processes within Siemens' operations.
AI helps Siemens optimize product designs. Machine learning algorithms analyze data from simulations and real-world use. This leads to better products with fewer prototypes needed.
In production, Siemens uses AI for predictive maintenance. Smart sensors and analytics forecast equipment issues. An AI system enables Siemens to analyze historical data and market trends, optimizing inventory management and meeting customer demand effectively. This approach has reduced unplanned downtime by up to 30% in some facilities.
Siemens also employs AI in quality assurance. Automated visual inspection systems catch defects humans might miss. This has improved product quality while speeding up production.
The company’s AI efforts have paid off. Siemens reports productivity gains of up to 25% in plants using these technologies.
Developing an AI Strategy for Manufacturers
Manufacturers need a clear AI strategy to stay competitive. This involves strong leadership, a forward-thinking vision, and smart investments to scale AI across operations. Additionally, optimizing manufacturing processes through AI can make operations more flexible and efficient, allowing for dynamic responses to market demands.
Integrating AI also requires considering the role of human workers. By collaborating with cobots, human workers can enhance productivity and safety, taking on repetitive or physically demanding tasks and ensuring a seamless workflow.
Leadership and Vision
Top executives must champion AI adoption. They should set clear goals for how AI will improve the business. These goals might include boosting productivity, cutting costs, or making better products. AI innovation plays a crucial role in leadership and vision, enhancing collaboration between humans and robots to make tasks safer and more efficient.
Leaders need to understand AI basics. They don’t need to be tech experts, but should know AI’s potential and limits. This knowledge helps them make smart choices about where to use AI. However, embedding AI within manufacturing workflows presents challenges, such as data quality and customization needs, which can discourage full integration despite its potential benefits.
A good vision links AI to the company’s main goals. It shows how AI fits into the big picture. This helps get everyone on board with AI projects.
Investment and Scalability
AI needs money and resources to grow. Manufacturers should start small with pilot projects. These test how AI works in real factory settings. Manufacturing companies are increasingly investing in AI to enhance various aspects of their operations, such as quality control, predictive maintenance, and supply chain management.
Successful pilots can then be scaled up. This means using AI in more areas of the business. It also means training more workers to use AI tools. AI agents play a crucial role in scaling AI projects by utilizing advanced technologies like AI and machine learning to optimize manufacturing processes.
ROI is key when investing in AI. Manufacturers should track how AI affects costs, quality, and output. This data helps justify more AI spending.
Companies need the right tech setup to scale AI. This includes good data systems and computing power. Cloud services can help smaller manufacturers access AI without huge upfront costs.
How to Implement AI in Your Factory?
Adopting AI in manufacturing requires more than just new technology—it calls for a thoughtful strategy. For companies looking to begin their AI journey, a phased approach can help reduce risk and maximize results. Here are five key steps to successfully implement AI in your factory:
1. Assess Current Data Infrastructure
Before introducing AI, evaluate your existing data systems. AI relies on clean, organized, and high-quality data from machines, sensors, and operations. Identify any gaps in data collection or connectivity that may limit the effectiveness of AI tools.
2. Start with Small, High-ROI Pilots
Focus first on projects with clear benefits, like predictive maintenance or quality inspection. These areas often deliver quick wins and measurable improvements, which help build internal support and justify further investment.
3. Build or Hire AI Talent
AI success depends on skilled people who understand both manufacturing and machine learning. Upskill your current workforce or bring in new talent with expertise in data science, AI modeling, and industrial systems integration.
4. Partner with Vendors or Integrators
Collaborate with AI solution providers or system integrators who understand your industry. These partners can accelerate deployment, offer technical support, and help tailor solutions to your factory’s specific needs.
5. Scale Proven Projects
Once pilot programs show results, expand them across more processes or sites. Standardize successful use cases and build the infrastructure to support broader AI adoption. Continuously measure performance and refine your approach as your AI capabilities grow.
By following this structured path, manufacturers can reduce complexity, improve ROI, and set the stage for long-term success with AI technologies.